Fleet Vehicle Maintenance: What Every Business Owner Should Know
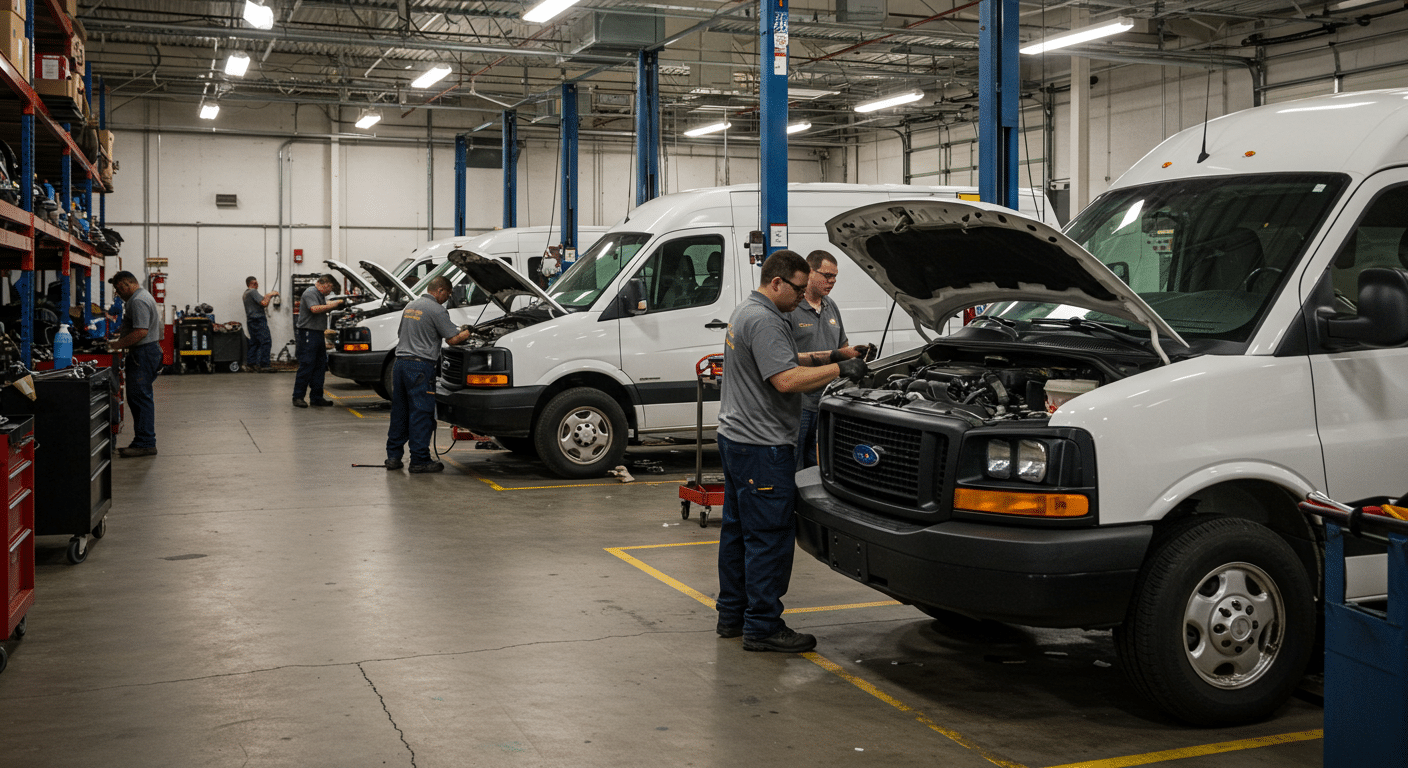
Sharing this:
Managing a fleet of vehicles is a substantial responsibility for any business owner. Whether you operate a small delivery service with a handful of vans or oversee a large-scale transportation company with dozens of trucks, proper maintenance is crucial to your operation's success.
Neglecting fleet vehicle maintenance can lead to unexpected breakdowns, costly repairs, significant downtime, and even safety hazards for your drivers and others on the road. For business owners focused on growth and day-to-day operations, vehicle maintenance might seem like just another task on an already overwhelming list.
That’s where trusted partners like Blue Ridge Automotive come in. Our comprehensive guide will walk you through everything you need to know about fleet vehicle maintenance, from creating preventive maintenance schedules to leveraging technology for better fleet management.
Avoid Expensive Downtime: Why Skipping Fleet Maintenance Costs More
The financial impact of poor fleet maintenance extends far beyond the immediate repair costs. When vehicles break down unexpectedly, the consequences ripple throughout your entire operation. According to a 2023 study by the Fleet Management Association, businesses lose an average of $760 per day for each vehicle that's out of commission, and that doesn't include the actual repair costs.
Neglected maintenance leads to decreased fuel efficiency, with poorly maintained vehicles consuming up to 15% more fuel than well-maintained ones. For a fleet of just 10 vehicles, this could translate to thousands of dollars in unnecessary fuel expenses annually.
Beyond the direct costs, consider these indirect expenses:
- Lost productivity when employees can't perform their duties
- Damaged customer relationships due to missed appointments or deliveries
- Higher insurance premiums resulting from preventable accidents
- Decreased vehicle resale value at replacement time
One Blue Ridge Automotive client discovered this reality the hard way. A local construction company had deferred maintenance on its work trucks to save money during a slow period.
When business picked up, three of their six vehicles experienced major mechanical failures within the same month, forcing them to rent replacement vehicles at premium rates while simultaneously paying for extensive repairs. What seemed like a short-term savings strategy ultimately cost them over $20,000 in unexpected expenses.
Build a Preventive Maintenance Plan That Protects Your Fleet
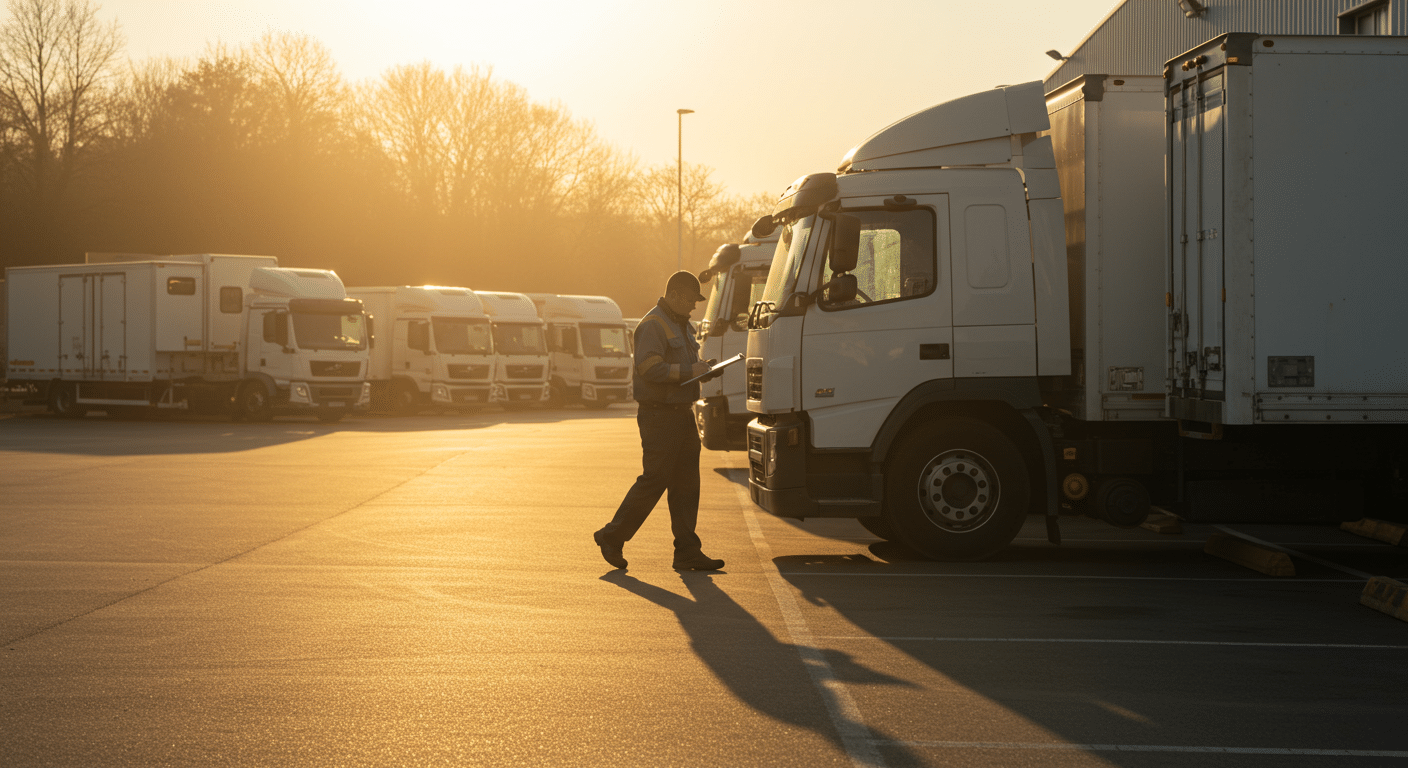
A well-structured preventive maintenance program forms the foundation of effective fleet management. Rather than reacting to breakdowns as they occur, preventive maintenance aims to address potential issues before they escalate into major problems.
The cornerstone of any preventive maintenance program is a clearly defined schedule based on vehicle type, usage patterns, manufacturer recommendations, and operating conditions. For most fleets, this includes regular oil changes every 3,000-7,500 miles (depending on the vehicle and oil type), tire rotations every 5,000-8,000 miles, and comprehensive inspections at manufacturer-recommended intervals.
Documentation is equally important. Every maintenance event should be recorded, creating a detailed service history for each vehicle. These records help identify recurring issues, track warranty coverage, and prove compliance with regulatory requirements. They also provide valuable data for making informed decisions about vehicle replacement timing.
Driver involvement is another critical element. Train your drivers to conduct basic pre-trip inspections and report any concerns immediately. Since they interact with the vehicles daily, drivers are often the first to notice unusual sounds, vibrations, or performance issues that could indicate developing problems. Empowering drivers to participate in the maintenance process creates a proactive culture of vehicle care throughout your organization.
Critical Maintenance Areas That Demand Regular Attention
Brake Systems
Your fleet's brake systems require special attention as they directly impact safety. The National Highway Traffic Safety Administration attributes approximately 22% of vehicle-related accidents to brake failures or inadequate brake performance. Regular brake services should include inspection of pads, rotors, calipers, and brake fluid levels.
Warning signs that indicate brake service is needed include:
- Squealing, grinding, or scraping noises
- Soft or spongy brake pedal feel
- The vehicle is pulling to one side during braking
- Vibration when braking
- Brake warning light illumination
For commercial vehicles, federal regulations specify minimum brake performance standards. Ensuring your fleet meets these standards isn't just about compliance; it's about protecting your drivers and the public.
Fluid Management
Fluids are the lifeblood of your vehicles. Engine oil, transmission fluid, brake fluid, coolant, power steering fluid, and windshield washer fluid all require regular inspection and replacement.
Engine oil should typically be changed every 3,000-7,500 miles, depending on the vehicle, driving conditions, and oil type. Transmission fluid generally requires replacement every 30,000-60,000 miles, though some modern vehicles may have extended intervals. Coolant should be flushed and replaced every 30,000-50,000 miles to prevent corrosion and overheating.
Proper fluid management significantly extends the lifespan of major components. For example, regular transmission fluid changes can help avoid transmission replacements that might cost $3,000-$5,000 per vehicle.
Tire Maintenance
Tires represent both a significant safety factor and a substantial ongoing expense for fleet operations. Proper inflation alone can improve fuel economy by 3-4% and extend tire life by up to 20%, according to the Department of Energy.
Implement a tire maintenance program that includes:
- Weekly pressure checks (including spares)
- Regular rotation every 5,000-8,000 miles
- Alignment checks at least twice yearly
- Tread depth monitoring
- Seasonal tire changes in applicable regions
Many fleet managers are now utilizing tire pressure monitoring systems (TPMS) to provide real-time alerts about underinflated tires, preventing blowouts and improving fuel efficiency.
Electrical Systems
Modern vehicles rely heavily on electrical systems, from engine management computers to safety features. Battery testing should be performed regularly, especially before extreme weather seasons. Most commercial vehicle batteries last 3-5 years; however, factors such as temperature extremes and frequent short trips can significantly reduce battery life.
Alternators and starters should be tested annually, and all external lights should be checked during driver inspections. Addressing electrical issues promptly can prevent the cascading failures that often occur when electrical systems begin to deteriorate.
Use Technology to Stay Ahead of Costly Vehicle Failures
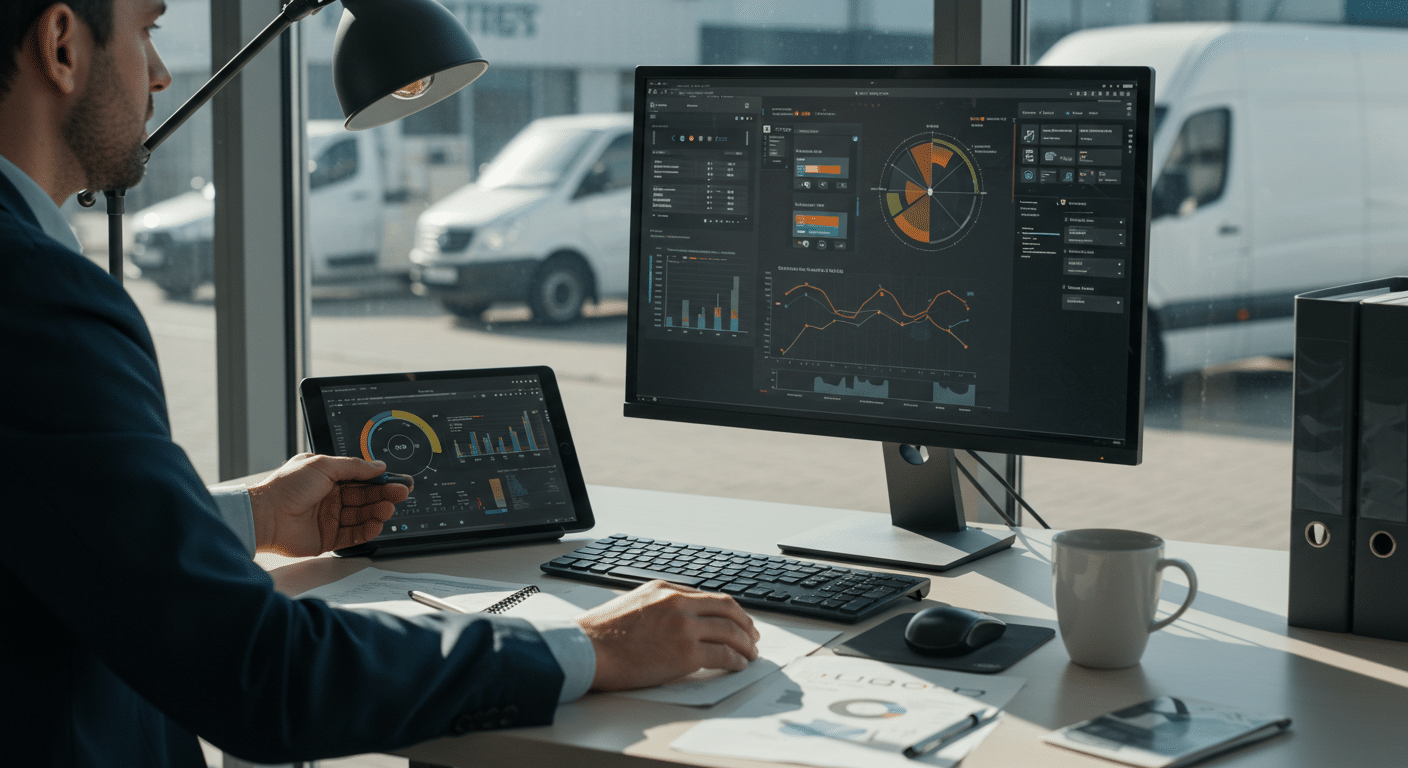
Technology has revolutionized fleet maintenance management, offering unprecedented visibility and control. Modern fleet management software provides comprehensive maintenance tracking, automated service reminders, and detailed reporting capabilities.
Telematics systems connect directly to your vehicles' onboard computers, transmitting real-time data about engine performance, driving behavior, and diagnostic trouble codes. This technology can alert you to developing issues before they cause breakdowns, allowing for scheduled maintenance rather than emergency repairs.
For example, one Blue Ridge Automotive client implemented a telematics system across their delivery fleet and received an alert about declining oil pressure in a vehicle that showed no obvious signs of problems.
Investigation revealed a developing oil pump failure that, had it gone unaddressed, would have resulted in catastrophic engine damage. The early warning saved them approximately $7,000 in repair costs and prevented potential delivery disruptions.
Mobile maintenance applications enable drivers to conduct and document digital vehicle inspections, report issues with photos, and even schedule service appointments from the field. These tools create accountability and ensure that minor problems don't go unreported.
Predictive maintenance algorithms analyze historical data and current vehicle conditions to forecast when components are likely to fail, allowing maintenance to be scheduled at the optimal time, not too early (wasting useful component life) and not too late (risking breakdown).
Partner with Experts to Keep Your Fleet on the Road
While some businesses maintain in-house service facilities, many rely on external service providers for their maintenance needs. Building strong relationships with qualified technicians who understand your business requirements can significantly improve your maintenance program's effectiveness.
When selecting service providers, consider these factors:
- Technician certifications and specializations
- Experience with your specific vehicle types
- Geographical coverage relative to your operating area
- Availability of emergency services
- Pricing structure and warranty policies
Establish clear communication protocols with your service partners, including preferred methods for authorization, documentation requirements, and invoice processing. Many service providers offer fleet accounts with streamlined billing and reporting, reducing administrative overhead.
Consider negotiating preventive maintenance packages that bundle common services at discounted rates. These arrangements can reduce both direct costs and the time vehicles spend in the shop.
Some fleets benefit from mobile maintenance services that perform routine maintenance at your facility, eliminating the need to transport vehicles to service centers. This approach minimizes downtime and keeps your operations running smoothly.
Turn Maintenance Insights into Fleet-Wide Visibility
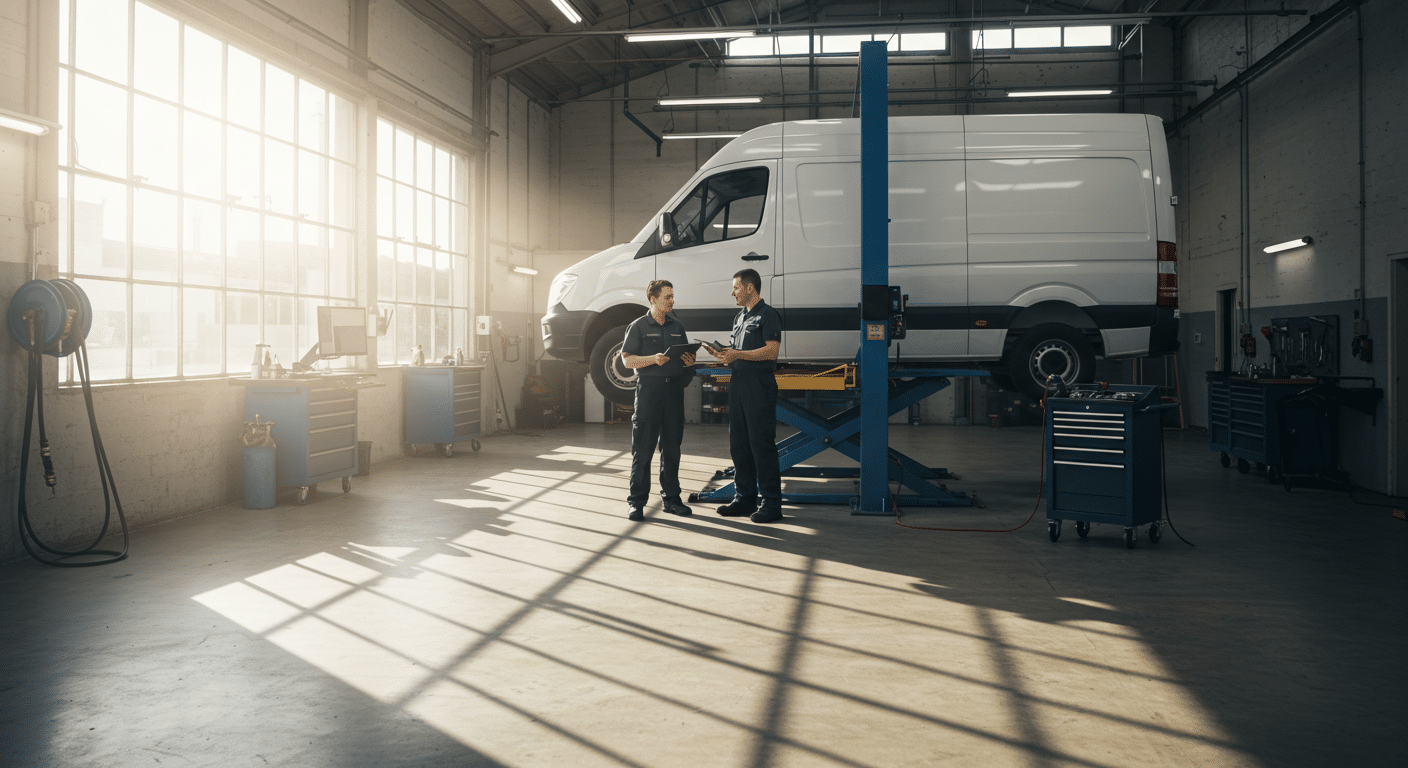
One of the most overlooked tools for improving fleet performance isn’t under the hood; it’s in the service records. Centralized maintenance documentation helps business owners and fleet managers see the bigger picture.
Instead of treating each repair as a one-off issue, detailed records turn your fleet into a data-driven asset. Patterns similar to recurring brake wear, early battery failures, or tire issues that are tied to specific vehicle types or driving routes emerge. With this visibility, you’re not just maintaining vehicles; you’re refining how your fleet operates.
Blue Ridge Automotive helps streamline this process. Every service we perform, whether it’s mobile maintenance, diagnostics, or emergency repairs, gets logged and tracked. You’ll have digital records for each vehicle in your fleet, accessible whenever you need them. This isn't just helpful during audits or inspections; it also supports smarter decision-making around repairs, replacements, and budgeting.
Plus, if multiple drivers share a vehicle or rotate across different units, these records create continuity. You won’t have to rely on memory or guesswork to understand a vehicle’s history; everything is recorded, up-to-date, and in one place.
This kind of clarity reduces downtime, avoids redundant service, and helps you stay ahead of compliance requirements. It’s a proactive way to manage your fleet without asking drivers to become mechanics.
Frequently Asked Questions
How often should fleet vehicles receive preventive maintenance?
Fleet vehicles should follow manufacturer-recommended maintenance schedules at a minimum, typically based on mileage intervals or periods. However, commercial vehicles often operate under severe conditions that warrant more frequent service.
Most fleet managers implement a schedule that includes oil changes every 3,000-5,000 miles, comprehensive inspections every 15,000 miles, and major service intervals (transmission, cooling system, etc.) based on manufacturer guidelines.
Vehicles used in harsh environments or for heavy-duty applications may require even more frequent attention. The key is creating a consistent schedule that accounts for your specific vehicles and operating conditions, then documenting all maintenance meticulously.
What are the most common maintenance issues for commercial fleet vehicles?
Brake system wear ranks as the most frequent maintenance issue for commercial fleets, particularly for vehicles that operate in urban environments with frequent stops. Electrical system problems, including battery failures and alternator issues, represent the second most common category.
Tire wear and damage are other prevalent concerns, especially for vehicles traveling long distances or on rough terrain. Suspension components, including shocks and struts, frequently require attention in fleets that regularly transport heavy loads.
Finally, cooling system failures remain common, particularly in older vehicles or those operating in extreme temperature environments. Addressing these areas proactively can significantly reduce roadside breakdowns.
How can I calculate the return on investment for a preventive maintenance program?
Calculating ROI for preventive maintenance requires tracking both costs and benefits. Start by documenting all maintenance expenses, including parts, labor, and administrative time.
Then measure key performance indicators like reduction in roadside breakdowns, decrease in major repair costs, improvement in fuel efficiency, reduction in rental/replacement vehicle expenses, and extension of vehicle service life.
For example, if implementing a $15,000 annual preventive maintenance program reduces your emergency repair costs by $25,000 and improves fuel efficiency by $8,000, your ROI would be substantial. Most businesses find that well-structured preventive maintenance programs deliver between 200-400% return on investment when all factors are considered.
Should I outsource fleet maintenance or build an in-house capability?
This decision depends on several factors, including fleet size, vehicle types, geographical dispersion, and available resources. In-house maintenance provides maximum control and potentially faster response times but requires significant investment in facilities, equipment, personnel, and training.
Outsourcing eliminates these capital expenditures and provides access to specialized expertise, but may result in less control over scheduling and quality. Many businesses adopt a hybrid approach, handling routine maintenance in-house while outsourcing specialized repairs.
For fleets with fewer than 25 vehicles, outsourcing typically proves more cost-effective, while larger operations may benefit from developing some in-house capabilities supplemented by strategic vendor relationships.
How can technology improve my fleet maintenance program?
Technology enhances fleet maintenance through several key mechanisms. Telematics systems provide real-time vehicle health monitoring, alerting you to developing issues before failures occur and collecting valuable data about vehicle performance patterns.
Maintenance management software automates service scheduling, tracks warranty coverage, maintains detailed service histories, and generates comprehensive reports for analysis. Mobile applications empower drivers to conduct digital vehicle inspections and immediately report concerns with supporting photos or videos.
Inventory management systems ensure that commonly needed parts are available when required, reducing vehicle downtime. Integration between these technologies creates a comprehensive ecosystem that significantly improves maintenance efficiency while reducing costs and vehicle downtime.
Create a Smarter Fleet Maintenance Strategy with Local Expertise
Implementing a comprehensive fleet vehicle maintenance program is not just about avoiding breakdowns; it's a strategic business decision that directly impacts your bottom line.
By prioritizing preventive maintenance, leveraging technology, building relationships with qualified service providers, and developing a maintenance-aware culture among your drivers, you can significantly reduce operating costs while extending vehicle lifespans.
The investment in proper maintenance pays dividends through improved reliability, enhanced safety, better fuel efficiency, and higher resale values. As you evaluate your current maintenance practices, consider consulting with automotive professionals who can help you identify opportunities for improvement and develop customized maintenance protocols for your specific fleet requirements and business needs.
About Blue Ridge Automotive
Blue Ridge Automotive delivers trusted fleet maintenance and repair services backed by over 25 years of experience in the Atlanta metro area. Our ASE-certified team handles everything from preventive care and brake service to diagnostics and emergency repairs.
Reach out today to learn how we can support your fleet with expert care tailored to your business needs. We offer flexible scheduling, mobile maintenance, and dedicated advisors to minimize downtime and keep your fleet running smoothly. With specialized equipment and detailed service records, we help you plan and avoid costly surprises.